Separation Systems
Industrial separation systems
Industrial ferrous separation systems - Applications, flange dimensions and technical notes
Iron is probably one of the most common materials in industry. But the presence of iron particles in raw materials, components or semi-finished products is totally unacceptable
especially in the food and confectionery industries. In most industrial processes, great care is taken to remove any unwanted ferrous contamination as thoroughly as possible. It seems obvious to state that this can be done with magnetism. One of the things BM has specialised in is the development and manufacture of industrial systems for removing ferrous contamination. The company's development department has been involved for many years now with industries facingthe problems of ferrous contamination. This effort has resulted in a great deal of know-how and the production of a wide range of highly specialised systems.
Raw materials can become contaminated with ferrous particles in many different ways. Shavings from milling operations, nuts and bolts that have vibrated free, burrs which have become detached from the metal components in transportation systems are just a few examples of the ways that contamination can occur. A universal solution for removing ferrous particles from all raw materials irrespective of the manufacturing system hasn't been discovered yet. The best solution for a specific problem is nearly always custom-made. For ferrous separation systems, we can identify a number of basic principles for particular systems and/or products each with its own characteristics. In addition, there is a extensive range of possibilities for the magnet systems themselves each of which influences the process in some way. In the standard specification, all systems are supplied with ceramic magnets. For extracting particles in the μ-region, the systems can be equipped with Neodymium magnets. In general it can be said that the best place for separating ferrous metals from raw materials in almost every situation is the transportation system. An efficient ferrous removal system can perform effectively without creating any noticeable delay to the
production process. BM also has a broad range of manual and automatic facilities for cleaning the ferrous separation systems.
Sanitary models
Various BM ferrous separation systems can be supplied in sanitary models which are especially suitable for the food industry and other applications where stringent hygiene standards are demanded. The sanitary systems are manufactured entirely from AISI 304 stainless steel, or they can be supplied in AISI 316 stainless steel if required. Particular attention has been paid to the surface treatment (stellated inside and outside). All of them are supplied with flanges conforming to the DIN 2576 ND 10 standard. Great care is taken during the design and manufacturing stages so that it is almost impossible for excess material to collect anywhere.
Several tips for using industrial ferrous separation systems
The magnet system in ferrous separation applications as used for raw materials is built from permanent magnets or electromagnets, plus other components some magnetically
conducting and others not. BM pays particular attention during the design and construction
of magnet systems to the design and dimensions of the various components. Even the combination of the various material properties is of utmost importance in arriving at a system with the best performance. To ensure that this excellent performance is retained in during operation, particular attention must be paid to the choice of components used when constructing the conveyor belt for use with the ferrous separation unit. For example, you shouldn't use any magnetically conducting materials in the operational area of the magnet system. If you do, these materials could become magnetised which would lead to accumulations of ferrous contamination in the wrong places or adversely influence the
efficiency of the ferrous separation process. Materials that can be used in the construction are, for example, aluminium, brass, stainless steel (AISI 300 series) and plastics. Bakker Magnetics' technicians will be pleased to advise you on integrating ferrous separation systems in your environment. In the construction of magnet systems, various magnetic materials can be used. The selection is made depending on the requirements which can
vary from situation to situation. Some of the groups of materials frequently used by BM are
explained in the following sections.
Ceramic
This magnetic material is used in many in ferrous separation systems. In normal use, a lifetime guarantee is given for its magnetic properties. The material can be recognised by its matt black colour.
AlNiCo
AlNiCo is an alloy made from aluminium, nickel, cobalt and steel. It is used in situations where great mechanical strength is required. The material is also able to withstand high temperatures and temperature changes. It is recognisable by its typical metallic appearance.
Samarium Cobalt
Samarium Cobalt is a powerful magnetic material made from rare earth minerals. It is almost impossible to demagnetise and always retains a very strong magnetic power. The material can be recognised by its dull metallic colour.
Neodymium
This is the strongest magnetic material currently available. It is used in situations which demand a very thorough ferrous separation. Bakker Magnetics uses this material in systems for separating ferrous contamination from raw materials in which very small particles (μ range) are present or the types of steel to be extracted have weak magnetic properties. Neodymium magnets can also be used successfully for ferrous separation from viscous fluids. Neodymium is a rare earth material.
Temperature stability of magnetic materials
Generally, the effectiveness of a magnet or a magnet system drops as the temperature rises. In practice, this has to be taken into account only rarely because most applications run at normal ambient temperature. However, every magnetic material has a critical temperature
at which its magnetic properties can be damaged.
Ceramic: 250° C
AlNiCo: 400° C
Samarium Cobalt: 250° C
Neodymium: 80° C
If the limits are not exceeded, the loss of magnetic power will only be temporary and the original magnetic power will be regained when it cools. Naturally, it is sensible to keep a good safety margin. For applications in which there is a chance that higher temperatures could occur, it is recommended to seek advice from BM in advance. Our extensive experience gained over many years in the application of magnet systems in industrial environments ensure the best solution for every ferrous separation problem.
DIN 2576 flanges
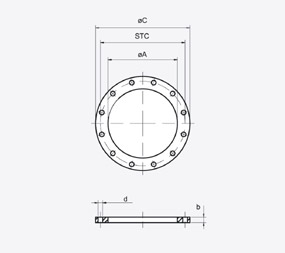
Various ferrous separation systems are fitted with flanges which conform to the DIN standard 2576 D10 NW. In particular, the sanitary models of the pipeline magnet systems are fitted with them. In the following table and illustration, the dimensions of the
various types are shown.